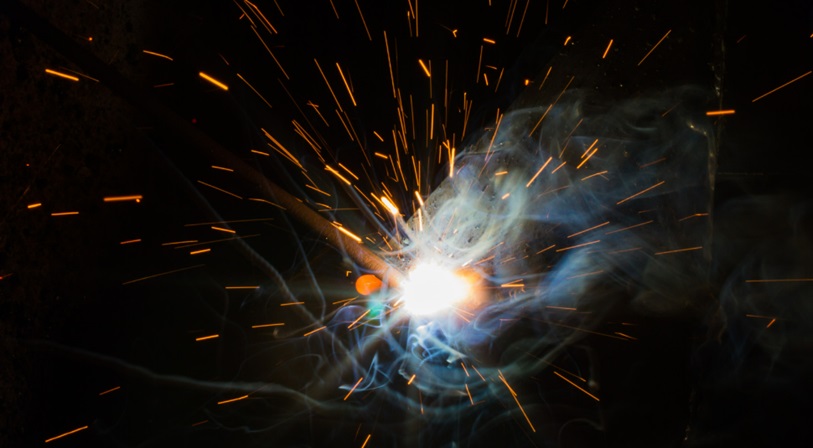
The Science Behind Welding Fume Extraction and Air Purification
Welding is a crucial process in many industries, but it comes with inherent risks to worker health and safety. One of the primary concerns is the generation of welding fumes, which contain potentially harmful particles and gases. To address this issue, the use of a welding fume extractor has become essential in modern welding environments. These devices are crucial in preserving air quality and safeguarding workers from the dangers posed by welding fumes.
Understanding Welding Fumes
Welding fumes consist of an intricate blend of metallic oxides, silicates, and fluorides. They are formed when metals are heated to their melting point, vaporize, and then condense into tiny particles. The composition of these fumes varies depending on the welding process, materials used, and working conditions. Common components include iron, manganese, chromium, nickel, and other metals.
Health Risks of Welding Fumes
Exposure to welding fumes can lead to both short-term and long-term health effects. Immediate symptoms may include irritation of the eyes, nose, and throat, as well as dizziness and nausea. Prolonged exposure has been linked to more serious conditions such as metal fume fever, chronic bronchitis, and, in some cases, an increased risk of lung cancer.
The Role of Welding Fume Extractors
Welding fume extractors are designed to capture and remove harmful particles and gases from the air at their source. These systems typically consist of three main components:
- Capture devices (hoods or nozzles)
- Ducting system
- Air cleaning device
The effectiveness of a fume extractor depends on its ability to capture fumes at the source, transport them away from the breathing zone, and efficiently filter out contaminants.
Types of Fume Extraction Systems
There are several types of fume extraction systems, including:
- Portable units for small-scale operations
- Fixed systems for larger facilities
- High-vacuum systems for confined spaces
- Low-vacuum systems for general area ventilation
Each type has its advantages and is suited to different welding environments and requirements.
Filtration Technologies
Modern welding fume extractors employ advanced filtration technologies to ensure high-efficiency particle removal. These may include:
- HEPA filters
- Activated carbon filters
- Electrostatic precipitators
Proper use and maintenance of these filtration systems are crucial for their effectiveness and longevity.
Innovations in Fume Extraction
Recent advancements in fume extraction technology include:
- Smart sensors for real-time air quality monitoring
- IoT-enabled systems for remote monitoring and control
- Energy-efficient designs to reduce operational costs
These innovations are making fume extraction systems more efficient, user-friendly, and cost-effective.
Regulatory Compliance and Standards
Welding fume extraction is subject to various regulations and standards set by organizations such as OSHA, NIOSH, and the American Welding Society. These guidelines establish permissible exposure limits and best practices for fume control in welding environments.
Future Outlook
As awareness of occupational health hazards grows, the importance of effective fume extraction in welding processes is likely to increase. Future developments may focus on more sustainable filtration methods, integration with personal protective equipment, and further automation of air quality management in welding facilities.
In conclusion, welding fume extractors are essential tools in modern welding operations, protecting workers’ health and ensuring compliance with safety regulations. As technology advances, these systems will continue to evolve, offering better protection and improved efficiency in the workplace.
Learn more about the importance of welding fume extractors and how they contribute to a safer welding environment.